wire drawing
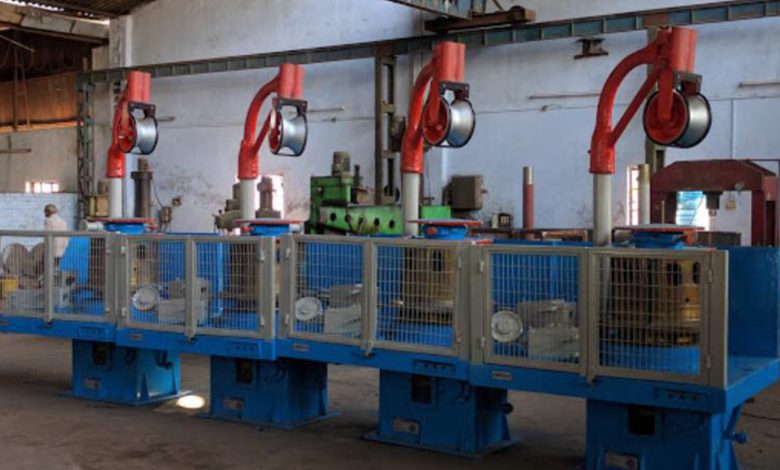
Metal stamping is a metal manufacturing process in which a cylindrical billet inside a sealed cavity is forced to pass through a die of the desired cross section. These extruded parts have a constant cross section called “stamping” and pushed out by mechanical or hydraulic presses. wire nail making machine
The most common extrusion materials are aluminum, copper, steel, magnesium, and lead. Plastics and ceramics are also extensively extruded but are not discussed in this article.
metal stamping Features
Capable of creating complex and uniform sections along the entire length of the extrusions
The factors affecting extrusion quality are die design, extrusion grade, workpiece temperature, lubrication and extrusion speed. Check detailed design instructions to force metal extrusion, “how to develop parts for simple metal methods” to understand 5 main variables and metal production designs (DFM). Like any other metal creation process, it can done hot or cold, although this process is usually done at high temperatures to reduce extrusion and improve material plasticity.
Low cost from reducing raw materials and high production speed
Fragile material can be deformed without cracks, because it only provides compression and moving in the warehouse
Details are created
Metal extract tends to create a favorable expansion of granular structure for materials. A minimum wall thickness of ~1 mm (aluminum) to ~3 mm (steel) can be achieved.
Types of metal stamping processes
Metal stamping can be divided and grouped into the following categories depending on the direction of the extrusion flow, the medium used to apply the force, the operating temperature, etc.
Direct Extrusion
Indirect extrusion
hydrostatic extrusion
Side or vertical embossing
hot stamping
Cold extrusion
extrusion impact
Direct Extrusion
Direct extrusion, sometimes called direct extrusion, is the most common type of extrusion.
The process is shown in below begins with loading a preheated billet (hot extrusion only, discussed below) into the press cavity container, followed by a dummy block. A mechanical or hydraulic piston is then pressed against the material to push it through the die. Then while it is still hot, the part is stretched to straighten it. This process is beautifully animated by Core Materials.
high temperature
During direct pressing, the high friction caused by the steel at higher temperatures is reduced by using molten glass as a lubricant, and graphite powdered oil is used for high temperature lubrication. short. End cap block is used to protect the end of pressure bar (punch or slider) during hot stamping. When the punch reaches the end of its stroke, a small part of the workpiece, called the “butt”, cannot be pushed out through the die opening.
The benefits of direct metal stamping
No need to modify the workpiece
It can use for both hot and cold extrusion.
Simple tooling compared to other extrusion processes
Disadvantages of direct metal stamping
High force requirement due to friction
The end is still inside the cavity
The force required to push the slider changes with the movement of the punch.
Indirect extrusion
In indirect extrusion, the die is located at the end of the hydraulic cylinder and moves towards the workpiece inside the cavity to push the material through the die.
This process uses less energy because the cartridge holds the workpiece static, so there is less friction with the workpiece. However, supporting the extrusion is difficult because the extrusion comes out of the die.
Benefits of indirect metal stamping/
===
Less friction and less energy
It can be used for both hot and cold extrusion.
Simple tooling compared to other extrusion processes
Disadvantages of indirect metal stamping
Extrusion part is difficult to maintain
Hollow plunger limiting applied load
hydrostatic extrusion
In hydrostatic extrusion, the chamber/cavity is smaller than the workpiece and filled with hydraulic fluid that transfers the force from the ram to the workpiece as shown in Figure 3. Although the fluid exerts a triaxial force, the pressure improves the deformability of the workpiece relative to the workpiece. Fluid sealing should be considered at an early stage to avoid leakage and pressure drop problems. ===
Although hydraulic liquid removes friction between walls and embryos, insulation, due to requirements for specialized equipment, high determination time and low production limit in the industry compared to other extrusion processes.
Advantages of hydrostatic metal extrusion
Low power/power due to lack of friction
Fast production indicators and high decreasing indicators
The temperature is lower than the item
Even a line of materials made of sustainable power
Large drum fields and large cross -sections can be touched
The rest of the embryo is not in the container
Remind hydrated metal. Defect
The pancakes must be prepared by narrowing one end to adapt to the corner of the entrance.
Can only extruded cold
It is difficult to prevent liquid under high pressure
Why deep prolonged production will give you a competitive advantage
A deep drawing offers some significant advantages of production compared to other processes. Deep drawing is one of the most popular sheet metal forming methods and is very valuable for large or long production orders. This process is used in various industries and involves the use of cheaper raw materials compared to other traditional methods. By using deep drawing, you are guaranteed to receive products with exceptional precision and detail.
Deep drawing uses less material in the manufacturing process, reducing costs but also waste. Other processes, such as rotation, require very significant waste costs.
wide range of materials
Deep drawing is suitable for a wide range of materials including; stainless steel, aluminum, galfan, nickel silver and brass, offering customers a wide selection of materials to meet their component needs. The deep drawing process also allows for the creation of complex and uncomplicated designs and without the need for costly extra operations such as punching, which again reduces production costs.
High temperature
As a precision engineering company, we specialize in manufacturing precision and precision parts and products; with deep drawing we can achieve it. Deeply drawn products that can meet rigorous standards and precision are reproduced in precise detail. Batch repeatability also ensures consistently high quality for high volume deep drawn parts. Thus, the risk of potential quality loss is reduced.
suitable for industries
Deep drawing has many advantages. Deep drawing is suitable for industries that require very specific and precise parts that can be manufactured from a wide variety of materials in short cycles.
Read more: Looking to get rid of pesky parasites? Iverjohn 6 mg (Ivermectin) may be just what you need!