Service Robot Sensing: Ultrasonic ToF, IMU, NTC
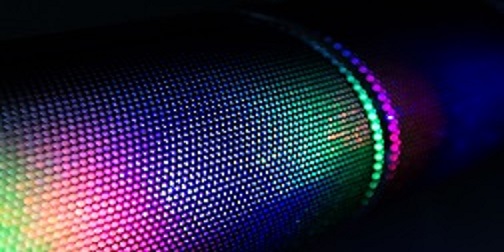
Any kind of robot has a huge demand for sensors. Various sensor combinations constitute the five senses of the robot and provide it with intelligent perception. Motion sensor for position detection, air pressure sensor for material detection, ultrasonic TOF sensor for obstacle detection, gas sensor and temperature sensor for indoor environment detection, a current sensor for battery current detection, Hall sensor and a magnetoresistive sensor for angle and position detection, etc. Wait. From sensing the outside to sensing the interior, these sensors completely cover the entire system of the robot.
Ground-type, high and low slope, and obstacle detection of ultrasonic ToF
In robot sensing, there are many methods we can use for obstacle detection, high and low slope detection, and ground detection. We have also talked about many sensing methods applied in this direction before, but today we take a look at ultrasonic ToF on-ground type, high and low slopes, and obstacle detection.
We all know that ultrasonic-based sensing is the most popular for robotics applications. Because it works under any lighting conditions, including full sunlight. Especially in sensing that the color and optical transparency of the object can not affect. Distance measurement can be accurate up to the millimeter level, a feature that many sensors cannot do. Ultrasonic ToF sensors utilize an ultrasonic transducer chip to transmit ultrasonic pulses. And then listen for echoes returning from targets located in the sensor’s field of view. By calculating the ultrasonic time-of-flight (ToF), the sensor can determine the position of an object relative to the device.
Here, the ultrasonic transducer chip is the top priority. The transducer chips under the MEMS process have been moving towards miniaturization and low power consumption. If it is only a single ultrasonic signal processing, it is obviously not enough to complete the detection of ground types, high and low slopes, and obstacles at the same time. In order to process a variety of ultrasonic signals, a single MEMS ultrasonic transducer is not enough. It is necessary to combine a MEMS ultrasonic transducer and a DSP on a mixed-signal CMOS ASIC. In order to process signals for a variety of different detection applications.
This type of ultrasonic ToF sensor needs to achieve a very wide FoV, and the sensing distance is not so critical. The FoV must be wide enough to allow multiple objects in the FoV to be covered at the same time. The use of ultrasonic ToF on-ground type detection can determine whether the target surface is “hard” or “soft”. We can widely use it in sweeping robots; obstacle presence detection and so on; the detection of high and low slopes usually requires the cooperation of multiple ultrasonic ToFs.
Calibration compensation for high precision IMU
IMU (Inertial Measurement Unit), the inertial measurement unit, is used to measure the three-axis attitude angle (or angular rate) and acceleration of the object.
It is also necessary for motion sensing of service robots, and a high-performance 6-axis is the first choice in the selection. In actual use, although high-performance IMUs are excellent enough in resolution, sampling accuracy, stability, and noise density, it is essential to compensate for the weaknesses of IMUs. These weaknesses mainly exist in the calibration of the IMU.
The first is to start the offset calibration of the robot IMU after the robot. At present, we emphasize programmable control generally. It is best to realize automatic or manual offset correction and to eliminate the initial error from the software level. With time and temperature changes, the IMU needs to dynamically calibrate the sensor bias drift that changes with time, and dynamically calibrate the temperature at all times, which is also a place to make up for it in real-time. Accurate motion-sensing must be based on real-time calibration. Each sensor has its own dynamic compensation formula. Most IMU chip manufacturers will complete all necessary motion detection and calibration during the production process, reducing the time and cost of reintegration.
In the data fusion processing in the actual use of the IMU, it depends entirely on the calibration capability of each manufacturer. The calibration capability of the offset drift determines whether the robot can track and estimate the motion direction correctly. For calibration that we require, the host must be able to provide the robot state to the calibration system. And the rate of processing the input data must be fast and can complete the response in a very short time. Which is very important for the motor MCU or motor. The control unit is also a test.
NTC trade-offs
NTC, we can also call it Negative Temperature Coefficient. It refers to the thermistor phenomenon and material whose resistance decreases exponentially with increasing temperature and has a negative temperature coefficient.
The NTC thermistor chip gives great support to the robot control in detecting temperature, especially the bondable NTC chip, which we use in the semiconductor device to charge the motor controller of the fixed battery state and the robot product. These NTCs are typically installed directly in the module and monitor the temperature of the semiconductor junctions. Power type thermistors are also used to suppress surges.
We widely use NTC thermistors in temperature sensing due to their cost-effectiveness, but they provide less accuracy at extreme temperatures. And the thermistor dissipates energy in the form of heat, which affects its measurement accuracy. The heat dissipated depends on the material composition and the current flowing through the device. If the requirement for the sensitivity and precision of the device is high, it’s better an NTC with low self-heating and small sensor drift.
In addition, in installation, in order to monitor temperature, screw-in sensors are more mature methods. Screw-in housings or metal labels can form this. Good thermal coupling.
write at the end
The robot has too many sensors, and we only select a few directions here. The perception ability of robots depends to a large extent on the key data provided by the sensing system. After combining ML and AI, robot perception has also begun to evolve in a more intelligent direction.