Business
Automated Packaging in the Transport Environment
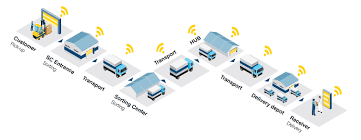
Having dealt with damaged goods in transit as a business End of line packaging automation, you are no doubt familiar with the difficulties that can arise as a result: disgruntled customers, returns and reimbursements, administrative time spent resolving the issues, and so on. Certainly, all of them are areas in which you wish you could spend less time End of line packaging automation!
A good place to start if you’re having these kinds of issues is to examine the way in which your pallet stacking and wrapping procedures are implemented. Pallet stability improves and transit damage is avoided when items are packed and wrapped properly.
Taking a quick look at the role of automation in the transportation packaging industry will be our topic for today’s post.
The Automated Palletizing System
Inconsistent and unstable pallet stacks are frequently produced by manual palletizing, which can result in articles being destroyed during transportation. Considerable risk of repetitive strain injuries exists, and the repercussions of workers being absent from work for extended periods of time, as well as the costs of any related claims, can quickly accumulate. Manual palletizing has the potential to limit throughput capacity and to operate as a bottleneck in your manufacturing process, according to the manufacturer.
Pallet stacking that is more uniform and neater as a result of automated palletising is more stable, as is the stacking of pallets overall. This is due to the accuracy with which the palletising system places the item on the pallet, which allows it to remain in the precise placement on the pallet. A more productive and efficient production environment is create by eliminating the need for breaks in an automated system. In most cases, an automated system increases throughput by at least 140 percent.
There are a plethora of automated palletising systems available on the market; therefore, it is vital to ensure that the system you choose will not only provide the immediate benefit of enhanced pallet stacking, but will also fulfil your long-term requirements. Make certain that the system provides an integrated stack builder that generates the optimum stack pattern for your product before implementing any of the features. The use of a system that has easy programming software allows you to rapidly and easily re-program the system to palletize boxes of varying sizes.
Pallet wrapping automation is becoming increasingly popular
Attempting to wrap pallets by hand may result in pallets that are not sufficiently firmly or securely wrapped. This, in turn, could result in shifting during travel, which could result in transit damage End of line packaging automation.
Pallets are wrapper securely and reliably when they are transport using an automated system, reducing the risk of shift during transportation and, as a result, transit damage. It also eliminates waste, which results in a reduction in costs. It is possible to use pallet wrapping automation as a stand-alone cell or as part of the palletising process.
In today’s market. There are a plethora of automated pallet wrapping systems available, therefore it is vital to ensure. That the solution you choose meets your requirements. If you make the right choice, you will be able to cut your pallet wrap expenses. Downtime due to pallet wrap changes, and waste by using less wrap per pallet.
Return on investment in automation
Installing an automated palletizing system can pay for itself in as little as a year and a half. If you have one employee at the end of a line who palletizes merchandise for one shift every day. The payback period is around three years. Alternatively, if you work three shifts. The payback period is significantly shorter at less than a year. When intangible benefits such as reduced risk of repetitive strain injury (RSI). Fewer transit damage claims, and so on are take into account. The payback time becomes even more favourable. You can use Grant’s automation payback calculator and intangible benefits calculator to help. You accurately predict the return on your investment in automation. Both tools are available for download. https://www.granta-automation.co.uk/resources
Other Automated Systems are also available
Another example of how automation can aid in the reduction of transit. Damage is the automation of container unloading and palletizing operations. Containers that are unload and palletized on a regular and proper basis. Offer greater pallet stability for storage and subsequent transport. Not only that, but it also improves efficiency by lowering. The need for human labor and increasing throughput at the same time. Using one of these technologies, Grant recently implemented. It for a big supermarket chain, resulting in a weekly savings of at least 119 man hours.
Summary
To summaries, automation of pallet stacking industradgroup. And wrapping methods is crucial for increasing pallet stability and reducing. The risk of transit damage throughout the shipping process. Installing an automated system typically. Has a payback period of less than a year in most instances.